What Factors Impact Shipping Costs and Delivery Times
- zachsievert15
- Nov 26, 2024
- 5 min read
Shipping costs and delivery times are critical considerations for businesses and customers alike. Understanding what drives these elements can help businesses manage their logistics effectively and keep customers satisfied. Below, we’ll explore key factors that affect both shipping costs and delivery times and provide insights into how businesses can optimize their shipping strategies.
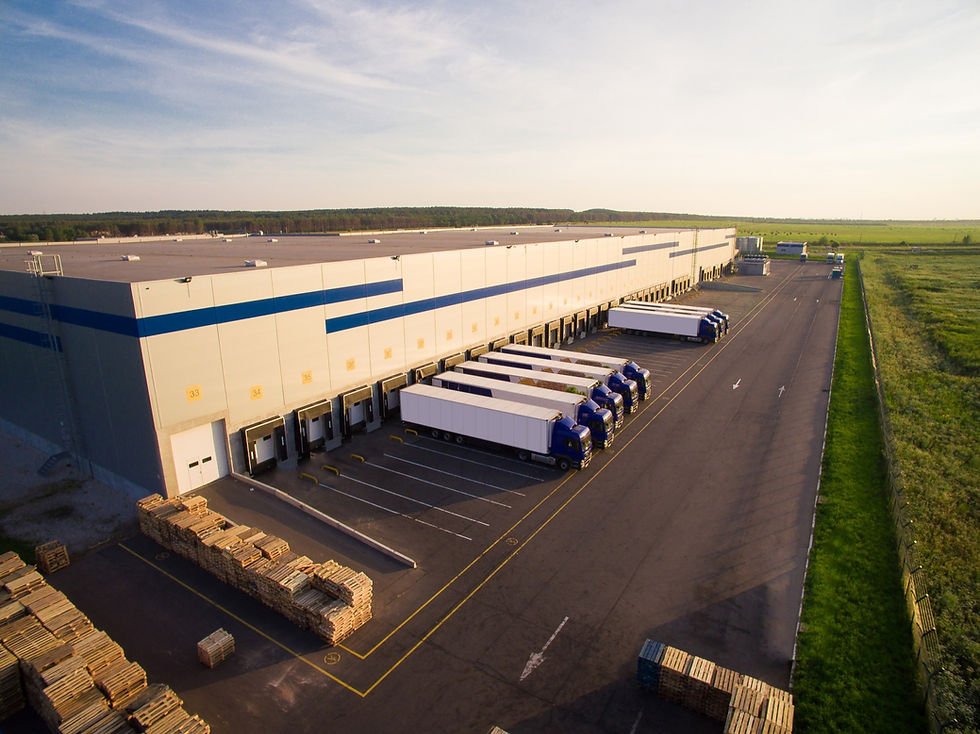
Key Factors That Impact Shipping Costs
One of the most significant factors impacting shipping costs is the size and weight of the package. Shipping carriers use dimensional weight (DIM weight) to calculate rates, which combines the package’s volume and weight. Larger or heavier packages naturally incur higher costs because they take up more space and require more resources to transport.
Businesses can reduce shipping costs by optimizing their packaging. Using smaller, lightweight materials not only saves on expenses but also minimizes environmental impact.
Distance and Delivery Zones
The distance a package needs to travel is one of the most obvious factors affecting shipping costs and delivery times. Carriers divide regions into shipping zones, with each zone representing a specific distance from the origin point. Packages traveling across multiple zones incur higher costs and longer delivery times compared to those shipped within the same zone.
For ecommerce businesses, understanding delivery zones can make a big difference. For example, a package shipped to a nearby state may fall into Zone 2 or Zone 3, resulting in lower costs. However, shipping to a destination across the country could place the package in Zone 8, significantly increasing the expense.
Companies can manage costs by analyzing their customer base and strategically locating inventory in an ecommerce warehouse close to their highest demand areas. This strategy, often called zone skipping, reduces the number of zones a package must cross and can lead to faster delivery times and lower shipping costs. Additionally, working with shipping and freight companies that have strong regional coverage can help further streamline deliveries.
Shipping Method
The choice of shipping method significantly affects both costs and delivery times. Different methods cater to various needs, and selecting the right one is essential for balancing speed and expense.
Standard Shipping
Standard shipping is the most economical option but typically takes the longest. It’s ideal for non-urgent deliveries where customers are willing to wait a few extra days. However, businesses should communicate clear expectations to customers to avoid dissatisfaction.
Expedited Shipping
Expedited shipping offers faster delivery times, usually within one to three days. While it appeals to customers who need their orders quickly, it comes at a premium cost. Businesses offering this option should carefully evaluate whether the additional expense is worth the potential increase in customer satisfaction and sales.
Freight Shipping
Freight shipping is used for larger, bulkier orders and involves transporting goods via truck, rail, air, or sea. This method is typically more cost-effective for heavy shipments, but the rates depend on several factors, such as the weight, size, and type of freight.
Understanding the difference between freight and shipping is crucial for businesses managing a mix of small and large orders. While freight shipping may involve pallets of goods or large containers, standard shipping focuses on individual packages. By choosing the most appropriate method for each shipment, businesses can optimize both costs and delivery times.

Seasonal Demand
Seasonal demand has a significant impact on shipping costs and delivery times. During peak seasons, such as the holidays, carriers face high volumes of shipments, which often leads to increased rates, capacity constraints, and potential delays.
For businesses, the key to reducing shipping delays during these periods lies in preparation. Advance planning, such as increasing inventory levels in fulfillment centers or partnering with reliable shipping and freight companies, can help manage demand. Additionally, businesses should communicate clearly with customers about expected delivery times to set realistic expectations.
Retailers can also consider offering incentives for early shopping, which helps spread out shipping demand over a longer period. For example, running holiday promotions in early November instead of late December can reduce last-minute shipping congestion.
Another factor to consider during peak seasons is the availability of carriers. Smaller businesses may struggle to secure capacity with major carriers when demand is at its highest. Partnering with a fulfillment company that has established relationships with carriers can help ensure packages are shipped on time, even during the busiest periods.
Customs and International Regulations
For international shipping, customs duties, taxes, and import regulations can significantly affect both costs and delivery times. Each country has unique requirements that businesses must adhere to, including documentation and product restrictions. Working with experienced fulfillment companies or freight forwarders can help navigate these challenges and ensure smooth international deliveries.
Carrier and Fulfillment Partner
Choosing the right shipping and freight companies has a direct impact on reducing shipping delays and ensuring fast and reliable shipping. Carriers vary in terms of pricing, reliability, and coverage. Similarly, fulfillment partners can make a difference by offering streamlined logistics and value-added services.
For example, ecommerce fulfillment providers often integrate technology to provide real-time tracking and ensure packages are delivered on time.
Fuel Prices and Surcharges
Rising fuel costs are another factor that affects shipping expenses. Carriers often add fuel surcharges to their rates, which fluctuate based on market conditions. While businesses can’t control fuel prices, they can compare rates from different carriers and consider consolidating shipments to reduce overall expenses.
Packaging Materials
The packaging materials businesses choose can impact shipping costs in several ways. Heavier materials, such as thick cardboard or bulky protective fillers, increase the package’s overall weight, leading to higher DIM weight calculations.
Opting for lightweight but durable materials can reduce shipping costs while still ensuring products arrive intact. For instance, replacing traditional bubble wrap with paper-based fillers or using smaller boxes that fit items snugly can save money and reduce waste.
Eco-friendly materials are gaining popularity, but they may come with higher upfront costs. However, businesses investing in sustainable packaging often gain customer trust and loyalty, which can offset these expenses in the long term.
Another aspect to consider is branding. Custom packaging with logos or designs can elevate the unboxing experience but may increase costs. Striking a balance between effective branding and cost management is key.

Why FlatOut Fulfillment Can Make a Difference
At FlatOut Fulfillment, we understand the challenges businesses face with shipping costs and delivery times. As one of the leading fulfillment companies, we offer tailored solutions to meet your logistics needs. Whether you're seeking fast and reliable shipping or looking to streamline ecommerce fulfillment, our team is ready to help you succeed.
Take control of your shipping strategy with FlatOut Fulfillment. Contact us to learn more about our services and how we can help you reduce shipping costs and improve delivery efficiency.